Accuracy is a crucial concern when performing a 3D laser scanning survey. During more than ten years of serving on point cloud data processing, our customers always come up with the same question: “Can we maintain a level of accuracy bounded by a few millimetres?”. So far, we have finished thousands of projects with similar job specifications, and the answer is, of course, yes. However, our customers and our team always sit together and explore another question before starting the project, and the question is: “Can we trust the current point cloud data”?
In this post, we first discuss several facts related to point cloud inaccuracies that are acquired by modern laser scanners. Then we demonstrate some real-world case studies about information loss during the laser scanning process. Finally, we suggest the solution to overcome these limitations to avoid any expected risks that compromise the quality of the final products—3D models, CAD drawings, visualizations.
The reasons for inaccuracies in point cloud capturing.
Errors in point cloud data may occur due to several reasons. The first reason is the inherent capability of the laser scanner. All laser scanners—even the best ones—have a maximum level of accuracy, and this level depends on the distance we measure. For example, the error is around +/- 1mm for every distance of 10 meters. Thus, the further the distance we desire to estimate, the larger the error could be incurred.
The second reason that leads to point cloud inaccuracies is the failure in the registration process. The registration process is sensitive to the initial alignment of the point clouds to be registered and their overlapping. Therefore, improper initial alignment or low overlapping scans may significantly damage the quality of the registration.
The final reason for point cloud inaccuracies is error propagation. This class of error happens when we combine multiple point cloud scans. For instance, we have a collection of point cloud scans, and each scan has an error of +/- 1mm. Thus, each step away from the rooted scan will suffer an accumulated amount of errors equal to the sum of square error by each scan.
Although there are many errors caused by not strictly following the best practices in fieldwork scanning, they are outside the scope of this post, as here, we mainly desire to share our experience on back-office data processing. We intend to share the best practices on fieldwork scanning in a future post.
Case studies.
Case study 1.
We describe the case study using a scan on the edge of a window—the edge divided the whole space into the inside half-space and outside half-space, as shown in Figure 1. We used some standard anchors as the reference points to assess the accuracy, and we found the deviation between the point cloud files of the outside half-space (FA_04) and the inside half-space (EG_64).
This deviation is about 40mm, but it is hard to identify. (if drawn according to the point cloud, the accuracy of 5mm does not hold true). The difference not only occurs between 2 point cloud files, but errors on nearby points are also detected in this example between—the file FA_04 and the file EG_62 in the figure below.
Similar deviation occurred between the file FA_029 and the file EG_60.
Case study 2.
Overall inspection we can find the door thickness left position is problematic compared to the same type of door on the right?
Zoom in on the left position
Zoom in on the right position
We figure out a huge deviation up to 90 mm. (if we draw according to point cloud, the accuracy of 5mm no longer makes sense). We further checked the vertical surface and it is clearly showed the difference in point cloud inside and outside space.
And many other deviations in different locations.
The Solution
Similar to other data processing pipelines, point cloud processing also deals with errors, and this phenomenon is normal. The important thing is how we address these kinds of information loss efficiently. Some argue that they could save time and cost for a customer by following a trivial workflow — they fill the erroneous data with the average values from its neighbouring points. Although this approach may save the processing time, the quality is severely sacrificed. This level of accuracy may be acceptable for specific purposes, including showcase, animation for advertising. However, it is not acceptable in critical domains such as construction and architecture.
We adopt a more rigorous verification process from the very beginning of the point cloud processing pipeline to overcome these issues. We are aware that the verification process may cause some overhead time. However, this is how we bring the highest quality to thousands of projects for customers worldwide. In particular, we integrated our workflow with the Kanban principle—the principle applied by Toyota corporation to maintain the consistency in the quality of their services. More precisely, at the beginning of the process, we get quick “feedback loops” with our customers until both of us “start to trust on our point cloud data”. Although we have the quality team to check for the deliveries, the data we use must be correct from the beginning, and that makes us stand out as one of the leading companies in point cloud data processing for more than ten years in the global market.
Take away
1/ We accept the fact that point clouds may have many deviations from reality, sometimes massive deviations.
2/ Some errors are notoriously hard to detect, and thus requiring a lot of know-how and hands-on experience in various complex projects.
3/ For this reason, verification is a must-have step in point cloud processing to make the data reliable before any further processing
FAQs
What are the common reasons for inaccuracies in point cloud data?
Inaccuracies in point cloud data can arise from several factors:
Laser Scanner Limitations: Even the best laser scanners have a maximum accuracy level that depends on the measurement distance. For instance, errors can be around +/- 1mm per 10 meters of distance.
Registration Failures: The process of aligning and merging point clouds can lead to inaccuracies if the initial alignment is improper or if there is insufficient overlap between scans.
Error Propagation: Combining multiple point cloud scans can accumulate errors. For example, if each scan has an error of +/- 1mm, the total error can increase with each additional scan.How can inaccuracies in point cloud data affect the final 3D models and CAD drawings?
Inaccuracies in point cloud data can lead to significant deviations in final 3D models and CAD drawings. For instance, deviations up to 40mm or more can occur, making the models less reliable. This is especially problematic for projects requiring high precision, such as construction and architecture, where even small errors can impact the overall quality and functionality of the final product.
What are the best practices for verifying point cloud data accuracy?
To ensure the accuracy of point cloud data, it is essential to follow rigorous verification practices:
Initial Verification: Conduct thorough checks of the point cloud data at the beginning of the processing pipeline to ensure it meets accuracy standards.
Customer Feedback: Engage in quick feedback loops with customers to address any issues and build trust in the data.
Quality Assurance: Implement a robust quality assurance process throughout the project to detect and correct errors promptly.How does VMT Solutions address point cloud data inaccuracies?
VMT Solutions addresses point cloud data inaccuracies through a meticulous verification process. We integrate our workflow with the Kanban principle to maintain high-quality standards and ensure that the data is reliable from the outset. By using continuous feedback loops and rigorous quality checks, we provide accurate and trustworthy point cloud data for all our projects, thus standing out in the global market for over ten years.
About the Author: Nguyen Huynh (Rainer)
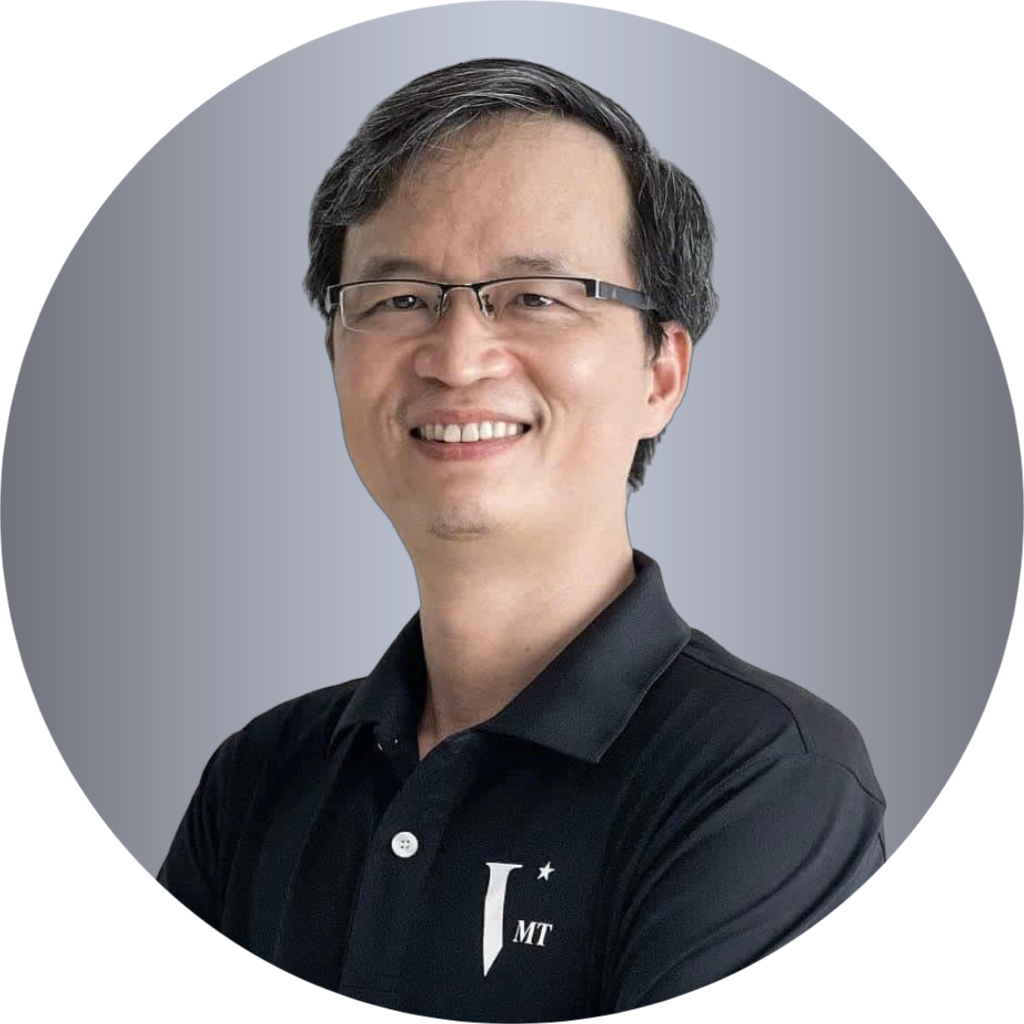
As the Co-Founder and CEO of VMT Solutions, I earned my Master’s degree in Technical and Vocational Education and Training (TVET) from Germany in 2007. With over a decade of experience in point cloud processing and BIM services, I’ve always been passionate about tackling complex challenges and developing innovative workflows that enhance accuracy and detail in point cloud to BIM conversions.
At VMT Solutions, we are committed to providing high-quality services that deliver exceptional value, particularly to surveying companies. We focus on building win-win relationships, ensuring that our clients benefit from tailored solutions that meet their specific needs. Every day, I strive to push the boundaries of our industry, continuously refining our methods and exploring new ways to optimize our offerings.
Recent Posts
Tag Cloud
We are proud to have
satisfied customers.
„Your plans are perfect; I’ve never seen anything like this before. These are drawings of the highest quality, I must say. I want to express my sincere thanks once again for your work.“
VMT modeled a large industrial building in 3D for our research project. We provided DWG plans to VMT, and they delivered a highly detailed model, including the building envelope, interior walls, openings, and stairs. We had previously contracted a German company for the same object, but unfortunately, it didn’t work out. I was relieved and pleased that VMT handled it so reliably. Thank you for the excellent work and the truly fair price!
Very reliable company, courteous staff, and top-quality work. Our plans were created quickly and accurately. Thank you for that. Highly recommended.
Excellent advice and high 3D modeling quality at a great price-performance ratio… What more could you want? I can highly recommend them…